Qualität
ISO9001-Zertifizierung
Bei Verbrugge steht Ihre Zufriedenheit an erster Stelle
Zertifizierte Qualität
Um die beste Qualität für seine Kunden zu gewährleisten, hat Verbrugge kürzlich erfolgreich seine ISO9001-Zertifizierung erneuert, die die Anforderungen an ein Qualitätsmanagementsystem für die industrielle Produktion festlegt.
Wenn Sie sich für Verbrugge entscheiden, profitieren Sie von einer vollständigen Rückverfolgbarkeit und einer perfekten Reproduzierbarkeit aller Ihrer Aufträge.
Wir sind in der Lage, auch die anspruchsvollsten Lastenhefte zu erfüllen.
Namhafte Kunden bestätigen regelmäßig durch ihre Audits die Exzellenz unseres Systems.
Arbeiten Sie mit uns zusammen
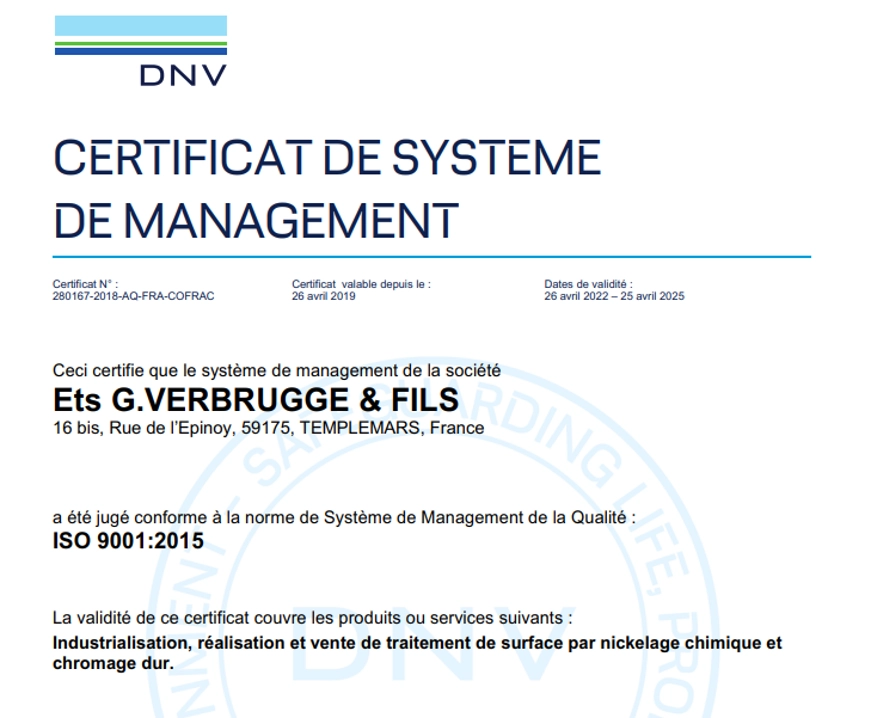
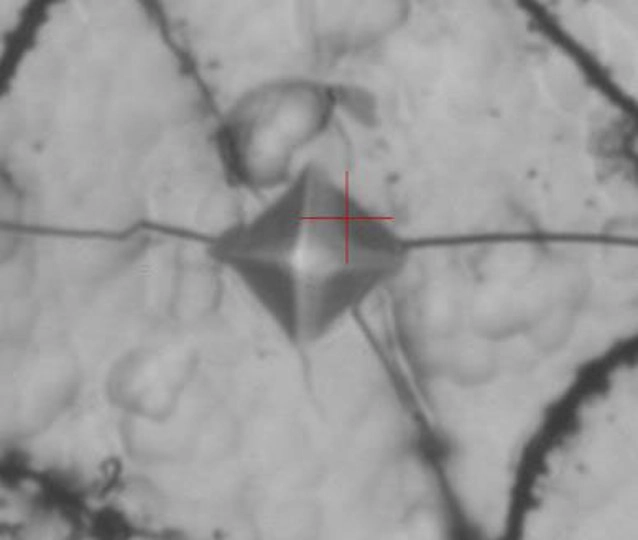
HÄRTEKONTROLLEN DURCH MIKRODUROMETER VICKERS LEITZ
Die Härte ist das Maß für den Widerstand eines Materials gegen das Eindringen einer konstanten und gleichmäßigen Kraft. Sie wird in der Regel mit einer Eindringhärte-Prüfmaschine ermittelt, bei der nach dem Entlasten die Größe der Diagonalen des Eindrucks gemessen wird, um so die Härte zu bestimmen.
Das härteste Material ist Diamant. Es ist so hart, dass es hauptsächlich als Eindringmaterial verwendet wird (Für Vickershärte HV).
Es gibt mehr oder weniger direkte Beziehungen zwischen Härte, mechanischer Festigkeit und Zähigkeit. Im Allgemeinen gilt: Je härter ein Material ist, desto höher ist seine mechanische Festigkeit, aber desto empfindlicher ist es auch.
Ein typisches Beispiel ist Gusseisen, das sich von Stahl durch einen kritischen Kohlenstoffgehalt unterscheidet, der zu Karbidausscheidungen führt, die das Material sehr widerstandsfähig und zugleich sehr empfindlich machen.
Zusammenfassend lässt sich sagen, dass der verwendete Begriff der „Festigkeit“ eines Teils nicht allein mit seiner Härte in Verbindung gebracht werden kann. Festigkeit wird in Bezug auf die Verwendung definiert. Die Wahl eines „festen“ Materials ist also immer ein Kompromiss zwischen Härte, mechanischer Festigkeit und Zähigkeit, zu denen je nach Verwendungszweck noch die Korrosions-, Ermüdungs- oder Kriechbeständigkeit hinzukommt.
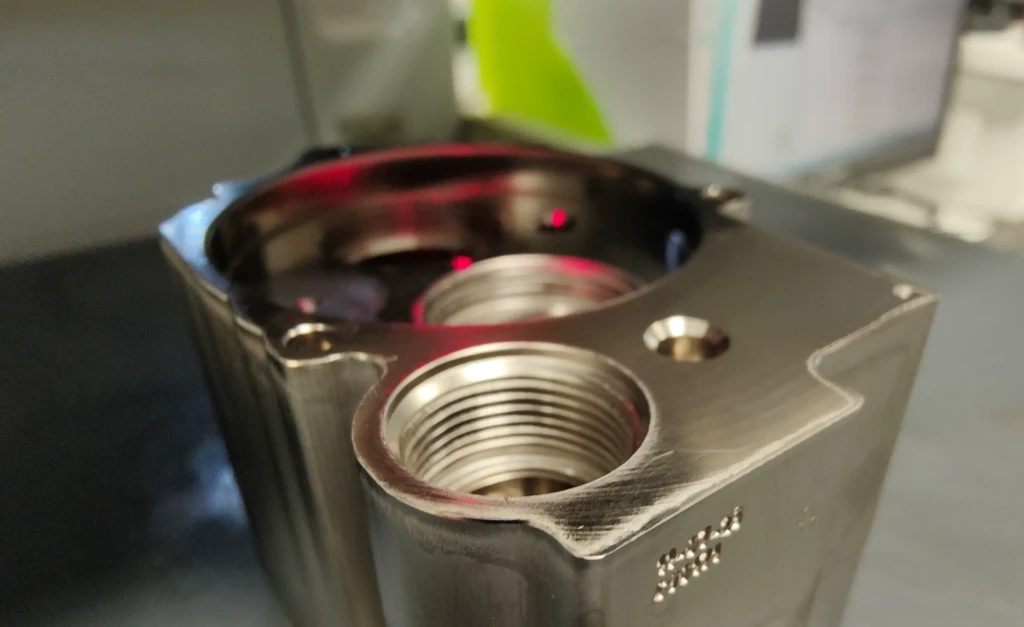
DICKENPRÜFUNG DURCH RÖNTGENFLUORESZENZ
Wenn ein Material fluoresziert, gibt es Energie in Form von Röntgenstrahlen ab: das ist die Röntgenfluoreszenz oder die sekundäre Emission von Röntgenstrahlen.
Das Spektrum der von der Materie emittierten Strahlen ist charakteristisch für die Zusammensetzung der Probe. Es ermöglicht uns, ihre elementare Zusammensetzung abzuleiten, d. h. die Massenkonzentrationen der Elemente, um die Dicke des Materials auf ein Mikrometer genau zu bestimmen.
Unser Fachwissen ermöglicht es uns, Nickel mit Röntgenfluoreszenz auf Dicke zu prüfen.
Eigenschaften:
– Kontrolle der Dicke von Beschichtungen von 2 μm bis 30 μm.
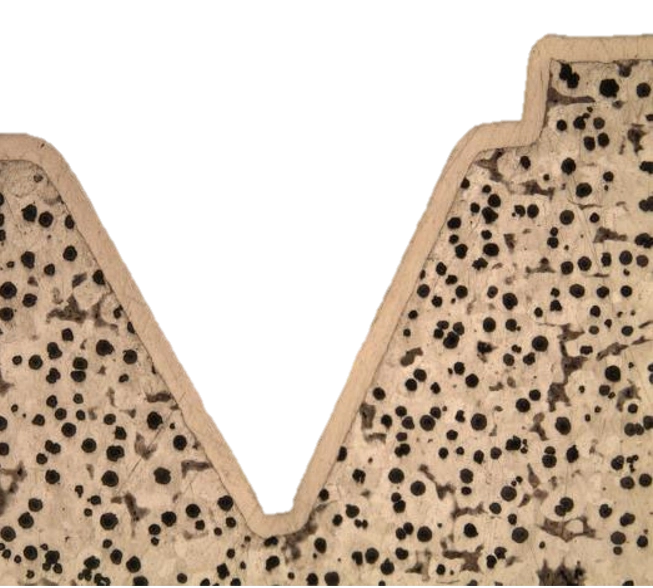
MIKROGRAPHISCHER SCHNITT
Die Kontrolle durch mikrographischen Schnitt wird an Proben durchgeführt. Im Bad platziert, folgen sie den Werkstücken bei ihren verschiedenen Behandlungen und erhalten so die gleiche Beschichtung.
Es handelt sich um ein Mittel zur zerstörenden Prüfung, das an einer Probe mithilfe eines Licht- und Elektronenmikroskops mit entsprechender Vergrößerung durchgeführt wird. Die Beschichtung wird durch einen Querschnitt des Werkstücks hervorgehoben.
Bei Verbrugge sind wir in der Lage, Kontrollen durch mikrographische Schnitte unserer Ablagerungen durchzuführen.
Diese Art der Kontrolle ist besonders informationsreich. Sie ermöglicht die Messung der Dicke einer oder mehrerer Schichten (sie können zwischen einem und mehreren Dutzend Mikrometern variieren), um die folgenden notwendigen Informationen zu erhalten:
– Ihre Homogenität, ihr mikrostruktureller Zustand, das Vorhandensein von Rissen, Porosität und Diskontinuität.
– Das Rauheitsprofil des Werkstücks und seiner Ablagerung.
– Die Qualität der Beschichtung, vor allem an scharfen Kanten und Ecken.
– Der oder die Ausfallmodi (Visualisierung des Schadensbildes, Schätzung der Angriffstiefe).
– Der metallurgische Zustand des Grundmaterials.
Eigenschaften:
– Strukturelle Kontrolle der Beschichtungen von 2 μm bis 500 μm.
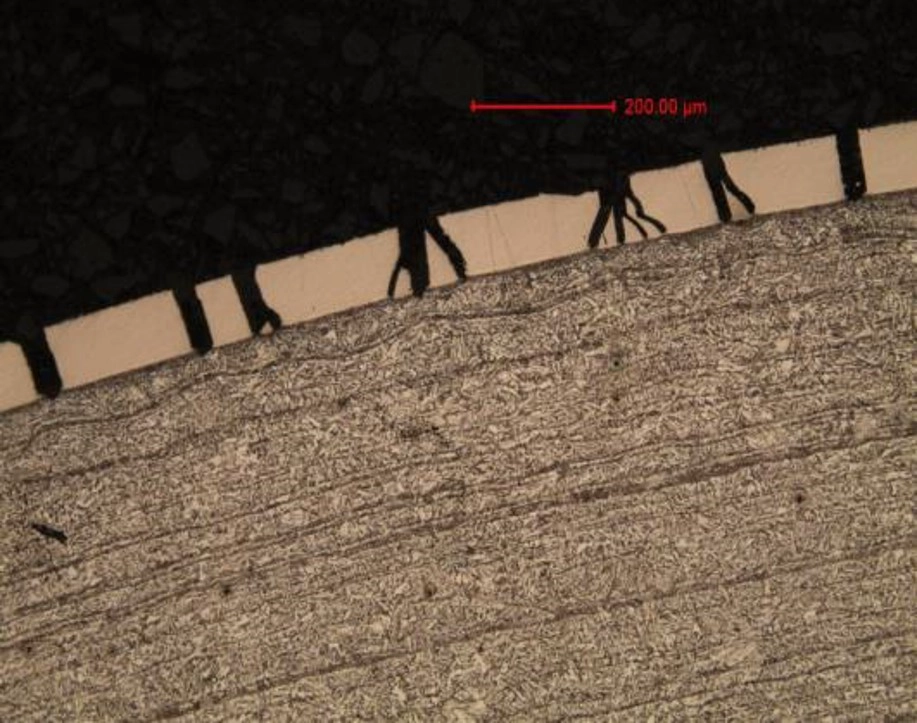
HAFTUNGSKONTROLLE
Die Haftfähigkeit ist ein kritischer Parameter für viele Anwendungen. Dieses Kriterium hat einen großen Einfluss auf das mechanische und tribologische Verhalten der Beschichtung sowie auf die dauerhafte Korrosionsbeständigkeit.
Je nach Art der Beschichtung und ihrer Verwendung sind die Haftfestigkeitsprüfungen mehr oder weniger streng. Im Allgemeinen ist der Begriff der Haftfähigkeit einer Beschichtung keine intrinsische Eigenschaft. Die Kontrollmittel bleiben im Wesentlichen qualitativ und an die Nutzungsbedingungen der Beschichtungen und Oberflächenbehandlungen angepasst.
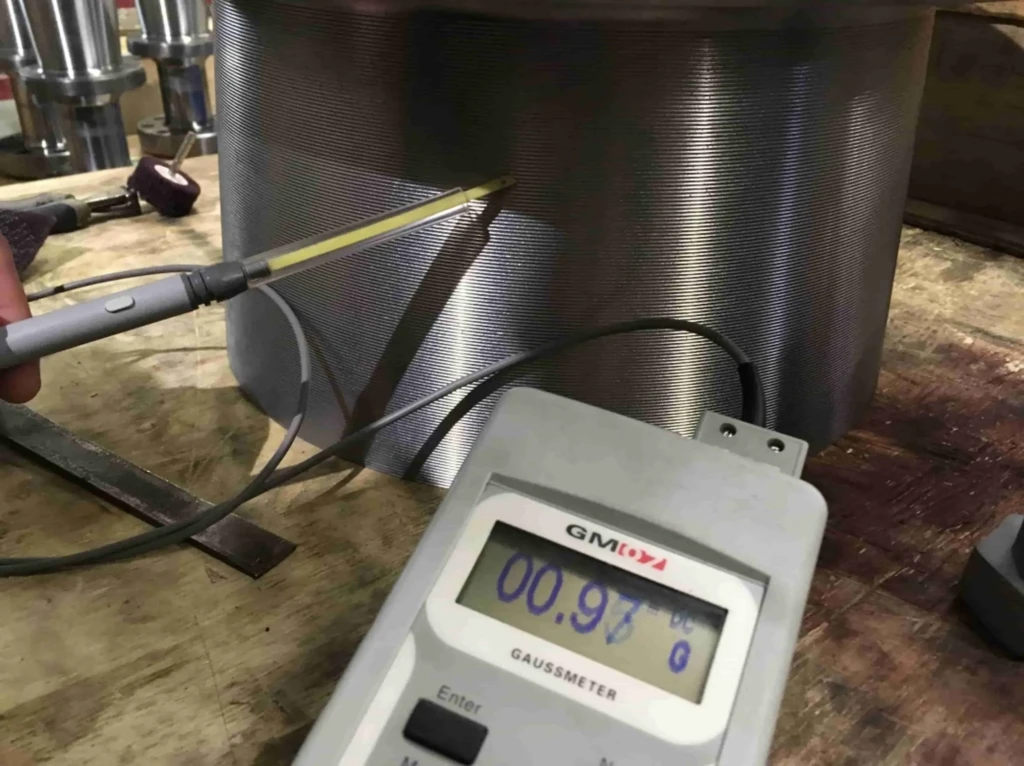
MAGNETISMUSKONTROLLE
Mit der Magnetismuskontrolle können Sie, wie der Name schon sagt, den remanenten Magnetismus Ihrer Bauteile feststellen. Die Messungen werden vor der Behandlung mit einem Gaussmeter vorgenommen, das über den gesamten zu behandelnden Bereich des Teils bewegt wird.
Teile, die selbst eine geringe Restmagnetkraft besitzen, verfügen nicht über eine Oberflächenbeschichtung von optimaler Qualität. Denn die Ablagerung neigt in der Tat dazu, nicht richtig zu haften und alle Verunreinigungen aus den Bädern aufzunehmen.
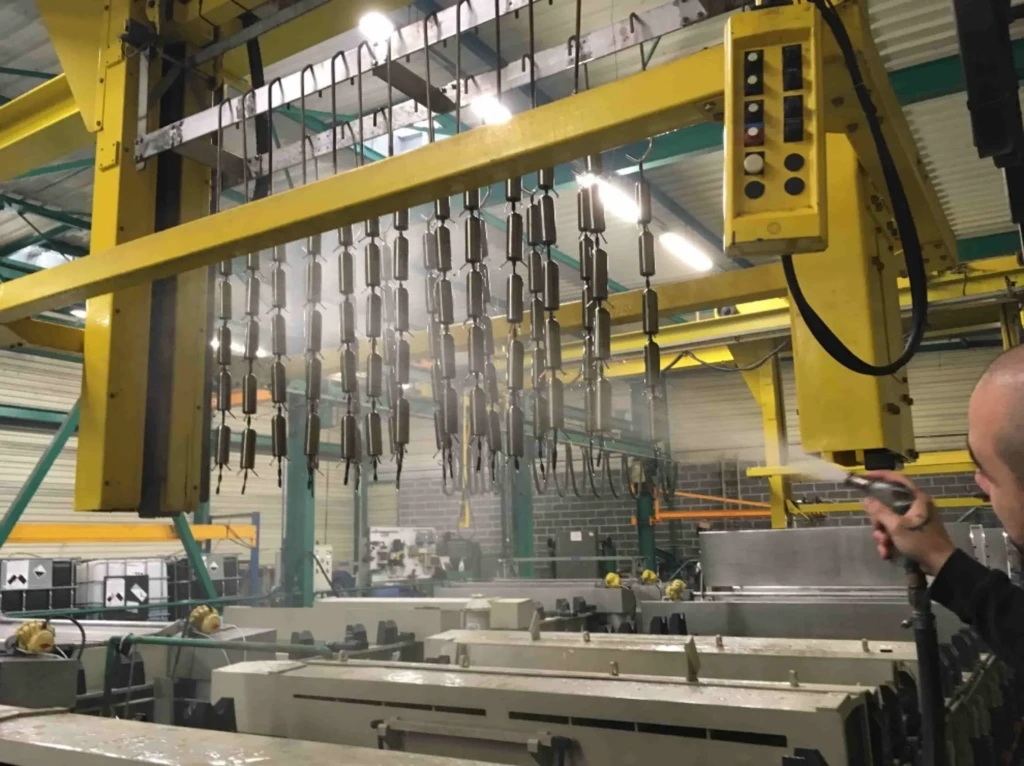
BENETZBARKEITSTEST
Der Benetzbarkeitstest ist visuell. Er dient in unserem Fall dazu, die Sauberkeit eines Teils zu testen, bevor es behandelt wird.
So führen wir bei der Ankunft bei uns (oder nach dem Entfetten) einen Benetzbarkeitstest durch, indem wir beobachten, wie sich ein Tropfen einer kalibrierten Flüssigkeit verhält, der auf die Oberfläche des Werkstücks aufgebracht wird: Je mehr sich der Tropfen ausbreitet, desto fettiger ist das Werkstück.
Dieser Test wird unter der Annahme durchgeführt, dass unsere Kunden Fette verwenden, die vor unserer Behandlung schwer zu entfernen sind.